
The new standard for tool applications
Published on:
2021-09-15
Tooling technology is evolving rapidly to meet changing demands and tougher challenges from workpiece materials. Today's job shop needs to revisit tools from a different perspective.
Tooling technology is evolving rapidly to meet changing demands and tougher challenges from workpiece materials. Today's job shop needs to revisit tools from a different perspective.
In the case of meeting various needs, the use of advanced tools can increase the machining capacity of the shop, such as the tool shown in Figure 1, which is from Diamond Innovations company for turning hard materials. Tool technology is developing rapidly, so choosing the right tool can essentially transform the process. In the metalworking industry, there is no alternative but to adopt advanced technology. In the future, the demand for machining will be huge, and only the use of advanced technology can meet this huge demand.
Taking the aerospace industry as an example, Mr. Chris Mills, project manager of the aerospace development department of Sandvik Coromant, pointed out that in order to meet the production needs of the aerospace industry in the next 20 years, its production and processing capacity must be tripled from now on. So how to achieve this goal?
To triple the machining capacity, would it be enough to simply triple the number of machining machines and still have the same machining process as it does today? That's not actually the case, he said. If the number of state-of-the-art machines is multiplied by 3, it means that the number of machine operators will also increase by the same multiple. Such a situation is simply unimaginable, because it is quite difficult for factories to hire qualified workers who are competent to operate processing machinery.
Therefore, triple the production capacity needs to be obtained from the continuous development of advanced technology, and only by this way can the existing number of metal processing operators monitor the large number of processing operations.
So where do these advanced technologies come from? Of course, these technologies also involve the development of the machine tool itself. Today, machine tools are becoming faster and more precise, however, the workpieces themselves are not evolving at the same incremental level, although they are also changing in nature. Today, the workpieces being machined not only have higher demands on their machining accuracy, delivery time and quality, but many workshops are also faced with an increasing number of difficult-to-machine materials that have never been encountered before. These materials include titanium alloys, nickel-based alloys, and compacted graphite cast iron (CGI), not to mention, in some cases, composite materials instead of metallic materials.
In other words, workpiece materials evolve faster and change more than the machines that cut them. There is a certain gap between machine tools and part materials, and in order to narrow or even exceed this gap, the fastest growing technology comes from metal cutting tools, and its development speed exceeds that of any other machining process.
Facts have proved that the development and change of tools are so great that no matter how large the processing and manufacturing plants are, they need to re-evaluate the processing ideas of their tools. It is not only necessary to re-examine the tool selection method, but also to reconsider some basic factors that affect the tool. But some of these core ideas are outdated, and the standard for knives has changed.
Recently, three major tool-related companies asked how shophouses should now think differently about tools. These companies are: Diamond Innovations, the world's leading supplier of cubic boron nitride (CBN) and polycrystalline diamond (PCD) materials for cutting tools; Precision Dormer, an alliance of two cutting tool companies with dozens of Has been providing specialized technology for efficient drilling and threading for many years; Sandvik Coromant - the world's first supplier of metalworking tools. All engineers from the three companies listed some of the main factors that currently have a fundamental impact on the nature and use of knives:
Challenging materials, including alternative materials and difficult-to-machine alloys. Some of these materials are less than 25% machinable as steel, and can cost hundreds of dollars per pound to process;
Parts with increasingly complex geometries, such as aircraft parts with thin walls and complex shapes;
There is an increasing demand for bulky parts, especially for turbines and various heavy equipment. The high-cost production of each part places more stringent requirements on the processing of these parts;
There are increasing demands for specialized quality and performance, such as for the fatigue strength typical of the surfaces of machined aircraft parts.
All these factors have prompted those leading machining shops to start considering related tooling issues. Diamond Innovations, Precision Dormer and Sandvik Coromant have identified five ways in which shophouses must think differently about their tooling technology and the companies that provide it. The 5 new criteria for tool selection are: improving machine efficiency, meeting the needs of application expertise, increasing the percentage of diamond tool applications, focusing on the largest source of expense, and tools should be considered from the outset.
Relevant news
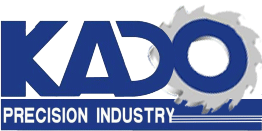
KADO Precision Industry Co.,Ltd
Tel: +86-769-85568865
Fax: + 86-769-85167115
E-mail: sales02@kadotool.com
sales03@kadotool.com
Add: No. 17, sifangyuan Industrial Zone, xinshapu, Huaide village, Humen Town, Dongguan City
copyright © 2022 Dongguan Guangrui Precision Hardware Technology Co., Ltd
Website by 300.cn | SEO